The Value of In-House Training: How We Get Employees Industry-Ready
- mwolverton3
- Apr 9
- 4 min read
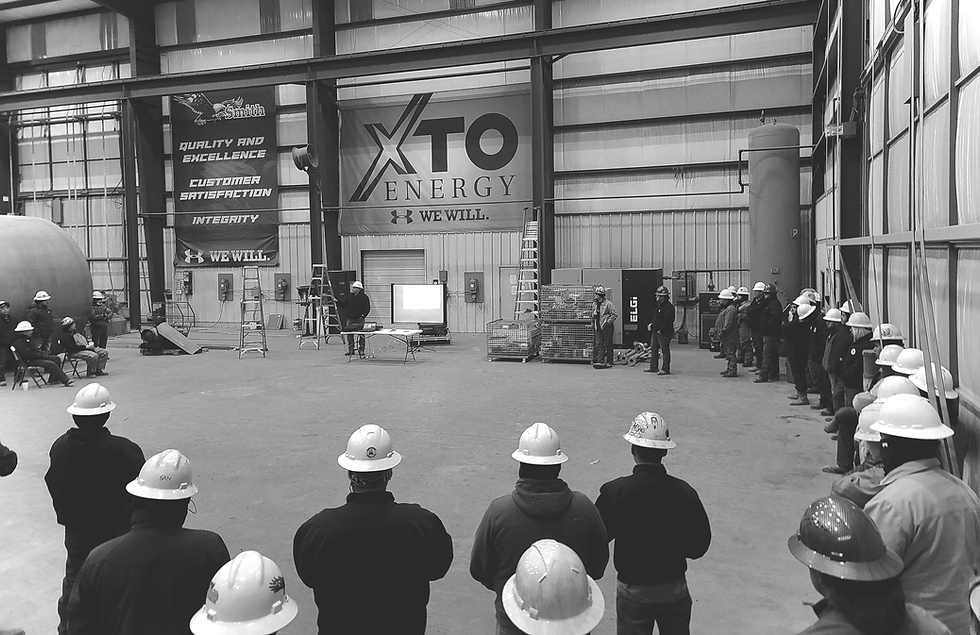
In the fast-paced world of fabrication and manufacturing, companies that prioritize workforce development often rise above the rest. At Smith Industries, that commitment begins the moment an employee walks through the door. With a strong emphasis on in-house training, safety awareness, and hands-on instruction, the company has created a system that builds reliable, skilled workers from the ground up.
From new hire orientation to advanced equipment handling, Smith Industries’ in-house training model is more than just a box to check—it’s a cornerstone of their operational excellence.
Why In-House Training Matters in Fabrication
In-house training refers to the practice of developing employee skills internally rather than relying on external certifications or programs. This method allows companies to tailor training to meet the specific needs of their facilities, tools, safety protocols, and customer expectations.
In the fabrication and oil & gas sectors, where one mistake can lead to costly downtime or injury, internal training programs help create a workforce that’s not only technically skilled but also aligned with company values, standards, and procedures. According to the Occupational Safety and Health Administration (OSHA), continuous, relevant training significantly reduces workplace incidents and contributes to a safer environment for all.
At Smith Industries, this isn’t just a theoretical concept—it’s a daily practice that starts with comprehensive onboarding and continues with regular skills development sessions.
Onboarding the Right Way: Orientation at Smith Industries
Every new hire at Smith Industries begins their journey with a robust orientation program. This isn’t just a general walk-through of policies—it’s a structured process that covers everything from hazard recognition to company-specific procedures. New employees receive instruction on how to identify potential dangers on job sites, how to react appropriately, and how Smith’s internal safety policies align with federal and industry standards.
That investment pays off in multiple ways. First, it promotes a culture of safety and confidence early on. Second, it creates a talent pipeline that understands the intricacies of Smith Industries’ operations, equipment, and workflow.
Apprenticeship: Building Talent from Within
Smith Industries doesn’t wait for workers to arrive with the perfect résumé. Instead, the company takes a proactive approach by offering apprenticeship programs that combine mentorship, technical training, and on-the-job experience.
This system allows new hires to move from basic tasks to specialized operations, such as pressure vessel fabrication or utility structure assembly, in just a few months. Supervisors guide apprentices through each step of the process, helping them learn how to read blueprints, operate machinery, and follow welding procedures that meet ASME and API standards.
According to the U.S. Department of Labor, companies that implement registered apprenticeship programs often see reduced turnover, increased productivity, and higher employee satisfaction. Smith Industries’ program isn’t just effective—it’s a testament to their belief in long-term workforce development.
In-House Safety Training
A defining feature of the in-house training at Smith Industries is the emphasis on routine safety education. The company holds regular meetings that cover a wide array of topics, including:
Personal Protective Equipment (PPE)
Fall prevention and ladder safety
Confined space protocols
Electrical safety
Hand and power tool safety
Lockout/tagout procedures
General awareness and hazard communication
Drug and alcohol workplace policies
Rather than treating safety as a one-time seminar, Smith Industries builds it into the fabric of daily operations. These recurring meetings foster a proactive attitude among employees and keep safety top of mind—whether someone is on a ladder, working in a confined space, or setting up heavy equipment.
It’s one thing to learn safety protocols in a classroom. It’s another to practice them daily under the guidance of trained supervisors and veteran fabricators. That’s the Smith Industries way.
Tailored for Success: Custom Instruction for Real-World Scenarios
Off-the-shelf training programs often fall short in environments where custom fabrication and diverse project scopes are the norm. By keeping instruction in-house, Smith Industries can design training that reflects the actual challenges and tools employees encounter on the job. Whether it’s learning how to prep a surface for blasting, operate overhead cranes, or follow quality assurance protocols, employees benefit from lessons tied directly to their work environment.
The company’s fabrication work spans multiple industries—from energy and utilities to oil & gas and heavy civil infrastructure—so training must be as diverse and adaptable as the projects they take on. That level of specificity would be impossible through external training programs alone.
Real Results: Confidence, Competency, and Culture
The return on investment for Smith Industries’ in-house training program is evident in the day-to-day performance of their crews. Employees who begin as general laborers quickly become confident operators, welders, or quality control technicians. The company’s commitment to this model has also created a sense of loyalty among the workforce.
By developing people from within, Smith creates opportunities for advancement that don’t require leaving the organization. It’s a win-win: workers build careers, and the company gains skilled professionals who understand the work, the values, and the expectations from top to bottom.
That culture of growth and support is one reason Smith Industries has been able to maintain a highly skilled and safety-minded workforce even in a competitive labor market.
Looking Forward: In-House Training as a Strategic Advantage
As fabrication continues to evolve with new technologies and more complex customer requirements, the companies that will thrive are those with flexible, capable teams. Smith Industries has embraced this truth by investing in a training infrastructure that turns raw potential into proven expertise.
Whether it's their apprenticeship program, routine safety meetings, or job-specific instruction, Smith Industries continues to raise the bar for what it means to be industry-ready.
In a world where talent shortages and safety concerns remain persistent challenges, Smith’s in-house training program stands out as a model worth replicating. It’s a reminder that when you build up your people, everything else follows.
Comments